Tests to Ensure the Quality of Fiber Patch Cords
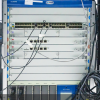
In order to provide customers with high quality fiber patch cords, manufacturers perform a series of tests during the design and manufacturing process. These fiber optic patch cord tests are critical to any type of fiber optic network. Not only suppliers, but also end-users need to understand these fiber patch cord tests to better judge the quality of fiber patch cords and to ensure the viability of their applications. This article will cover four types of tests: 3D testing, insertion loss (IL) testing and return loss (RL) testing, as well as endface testing. Usually after these four tests fiber patch cords are of high quality and can be used with confidence by end users.
3D test: the guarantee of high quality connector endface
3D testing is a critical test to ensure the performance of fiber optic connectors. When manufacturing fiber optic patch cord assemblies, suppliers will use 3D interferometer (an optical interferometry instrument) to check the fiber optic connector endface and strictly control the dimensions of the connector endface. 3D testing mainly measures the radius of curvature, vertex offset and fiber height. Details are as follows.
Radius of Curvature
The radius of curvature is the radius from the core axis to the endface, as shown in the figure below, which is the radius of the curve of the collar endface. The radius of curvature of the end face of a high quality fiber optic patch cord connector should be controlled within a certain range. Too small a radius of curvature will put more pressure on the fiber, while too large a radius of curvature will not be able to put pressure on the fiber, resulting in an air gap (i.e., air gap) between the connector and the fiber endface. Either too large or too small a radius of curvature will result in light scattering or insufficient physical contact to ensure optimal transmission performance. Only a proper radius of curvature will ensure proper pressure application and optimal transmission performance.
Vertex Offset
The apex offset is the distance from the highest point of the core end curve to the axis of the fiber core after grinding and polishing. This is a critical item in the polishing process, and inaccurate polishing will result in apex offset.
In technical standards, the apex offset of fiber patch cords is generally required to be ≤ 50 μm. If the apex offset is large, an air gap will be formed, resulting in high insertion loss (IL) and return loss (RL) of the fiber optic patch cord. Ideally, the apex offset of PC-type and UPC-type fiber optic connectors is almost zero, because they polish the collar end face perpendicular to the polished surface and the apex coincides with the core axis. However, for APC class fiber optic connectors, the end face is at an 8 degree angle to the fiber axis, which is not perfectly perpendicular.
Fiber Height
Fiber height is the distance from the fiber end face to the core section, which is the extension height of the core to the end face of the collar. Again, the height of the fiber cannot be too low or too high. If the height of the fiber is too high, the pressure inside the fiber will increase when mating the two fiber connectors, thus damaging the fiber; if the height of the fiber is too low, the gap will be created when mating the two fiber connectors, resulting in increased insertion loss. This is important to avoid for transmission with strict insertion loss requirements.
Different polishing methods and types of fiber patch cords will have different values tested with 3D interferometer, but all tested fiber patch cords should meet or exceed the industry accepted end face geometry standards. The following table shows the geometry requirements for MTP singlemode fiber optic connector endfaces based on IEC / PAS 61755-3-31 and IEC / PAS 61755-3-32.
Fiber Optic Radius of Curvature (RF)
Items | Requirements |
---|---|
Collar X angle (SX) | -0.2~0.2°(PC and APC) |
Collar Y angle (SY) | ±0.2° |
Collar X radius (RX) | ≥2000mm |
Collar Y radius (RY) | ≥5mm |
Fiber curvature radius (RF) | ≥1mm |
Fiber height (H) | 1000~3000nm |
Maximum fiber height difference (HA) | 500nm |
Maximum adjacent height difference (HB) | 300nm |
Coplanarity | ≤2000nm |
Core dip angle | -100nm~+ 200nm |
IL and RL Testing: Critical Tests For Optical Deployment
Insertion Loss (IL) is the loss of signal power that occurs somewhere in the transmission system due to the insertion of a device. Return Loss (RL) is the power loss that occurs when part of the signal is reflected back to the signal source due to discontinuities in the transmission link. For more information on the definition of insertion loss and return loss, please visit “An Analysis of Fiber Optic Connector Insertion Loss and Return Loss”.
Insertion loss and return loss testing is very important in both the manufacturing and installation processes. For fiber optic cable suppliers, the insertion loss and return loss of the provided fiber patch cords should comply with the corresponding standards. For example, the TIA standard clearly regulates the maximum insertion loss of fiber patch cords is 0.75dB (which is the maximum acceptable). For most fiber patch cords on the market, the normal range of insertion loss is between 0.3dB and 0.5dB, with some low insertion loss ranges between 0.15dB and 0.2dB. For fiber manufacturers, insertion loss testers and return loss testers are usually used to check if they are within the normal range so that the end user can receive a qualified product.
For end users, in addition to using the insertion loss and return loss values shown in the product specification sheet as a reference for designing fiber optic links and selecting other equipment or components, they can also perform their own tests if test tools are available. This effectively helps installers to quickly troubleshoot and identify faulty system components. Optical Time Domain Reflectometer (OTDR) and Optical Frequency Domain Reflectometer (OFDR) are both commonly used to measure return insertion loss.
Endface Testing: Ensuring Endface Cleanliness and Smoothness
By fiber cleanliness, we mean the cleanliness of the fiber connector endface. Both forty years ago and today, fiber connector endface cleaning is an essential step in fiber maintenance. Manufacturers typically perform an endface inspection using a fiber endface tester to verify that there are no contaminants, scratches, or breaks on the end face of the fiber connector. For fiber optic engineers, fiber optic cleaning tools (e.g. fiber optic cleaning pens, cassette cartridges, etc.) are often used to clean the fiber optic end face during cabling to ensure it is free of contamination.
Why is endface testing necessary? Because having a good fiber optic connector endface is essential to ensure a high quality fiber optic connection. If there are contaminants (e.g. dust, etc.) or scuffs or even deformed fiber optic connector endfaces, they will increase return loss and may even permanently damage the fiber optic connector, making it unusable. In addition, dust between the end faces can scratch the surface and cause air gaps or cores to fail to align, thus reducing the quality of optical signal transmission. Since these contaminants cannot be identified with the naked eye, they can contaminate the jacks to which they are connected if the endfaces are not tested and cleaned. Therefore, even if the supplier has tested and cleaned the end face of the fiber optic connector before shipment, the end face of the fiber optic connector needs to be cleaned before and after each insertion and removal. Also, if it will not be used again for a while, the end face should be covered with a dust cap.
Conclusion
In summary, the fiber optic industry has been exploring the key parameters that need to be measured to improve the quality of fiber optic connectors, and industry associations and committees have been working to define manufacturing standards for fiber optic quality assurance. If fiber patch cords pass these four tests and the results meet the standards, they will help achieve high quality optical signal transmission. For the end user, it is up to the supplier to check that these tests are performed and that the test reports are available to confirm that the values are within the correct range.